一、传统模具管理为何难以应对工业4.0挑战?
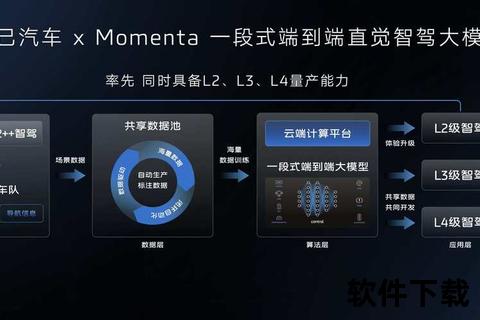
模具是制造业的“工业之母”,但长期以来,模具管理依赖人工记录、纸质单据和条码扫描的传统模式,导致效率低下、成本高昂。某调研数据显示,仅因模具定位错误导致的生产线停工,每年给中小型制造企业带来的损失高达数百万。而工业4.0时代,生产周期缩短30%、定制化需求激增的背景下,传统管理模式已显疲态——这是否意味着模具管理必须经历一场智能革命?
在青岛双星集团的智能化转型中,这一问题得到了验证。该企业曾因模具分散管理导致设备维护滞后,每月平均停机时间超过50小时。引入西门子数字化套件(PLM+MES+TIA)后,通过物联网传感器实时采集模具状态数据,结合AI算法预测维护周期,成功将停机时间压缩至8小时以内,模具利用率提升35%。这一案例揭示:智能革新驱动模具管理软件高效协同新纪元的核心,在于将“人找数据”转变为“数据找人”。
二、数据孤岛如何被智能协同击破?
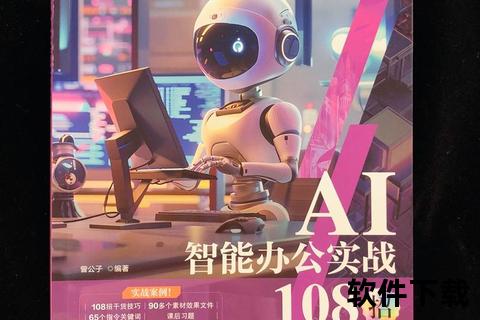
模具管理涉及设计、制造、维护等多个环节,但部门间数据割裂常导致决策滞后。例如,某汽车配件企业因设计部门与生产车间的数据不同步,导致模具修改重复率达40%,项目周期延长两个月。如何打通信息壁垒?
答案在于云端协同与全生命周期管理。以卡奥斯COSMOPlat模具物联平台为例,其通过“一物一码”的RFID技术,实现从模具设计图纸到报废回收的全流程追溯。某家电企业接入该平台后,模具调拨响应时间从48小时缩短至2小时,库存周转率提升60%。更值得关注的是,这类平台通过API接口与企业ERP、CAD系统无缝对接,使设计变更能实时触发生产排程调整,真正实现“数据驱动决策”。
三、预测性维护如何重塑行业成本结构?
模具维护成本占总生产成本的15%-20%,但传统“故障后维修”模式让企业陷入被动。浙江某注塑模具厂曾因关键模具突发故障,导致整条生产线瘫痪3天,直接损失超百万元。而智能管理软件通过三大革新改变这一困局:
1. 状态感知:NB-IoT终端每10秒上传模具温度、压力等参数,精度比人工检测提升90%
2. 算法预测:如模德宝系统通过分析合模次数、成型周期等200+指标,提前14天预警潜在故障
3. 资源调度:eMan制造执行系统自动匹配维修人员、备件库存与设备空闲时段,使维护效率提升70%
广东某电子配件企业的实践更具代表性:接入智能管理系统后,模具平均寿命从8万次冲压提升至12万次,年度维护成本下降42%。这印证了智能革新驱动模具管理软件高效协同新纪元的核心价值——从成本中心转变为利润引擎。
未来已来:企业如何踏上转型快车道?
面对智能管理浪潮,制造企业可采取三步走策略:
1. 评估现有痛点:优先解决模具盘点效率低下(推荐RFID方案)、维护响应迟缓(部署预测性算法)等高频问题
2. 选择适配系统:中小型企业可尝试Worktile等通用协同平台,大型集团则需定制化开发(参考双星PLM-MES集成经验)
3. 培养数字基因:建立数据中台团队,将模具使用数据与生产、供应链系统深度融合
某行业协会预测,2025年全球智能模具管理市场规模将突破120亿美元。在这场智能革新驱动模具管理软件高效协同新纪元的变革中,先行者已收获红利,后来者更需把握窗口期——因为未来工厂的竞争力,正藏在每一台联网模具的实时数据流中。
文章已关闭评论!